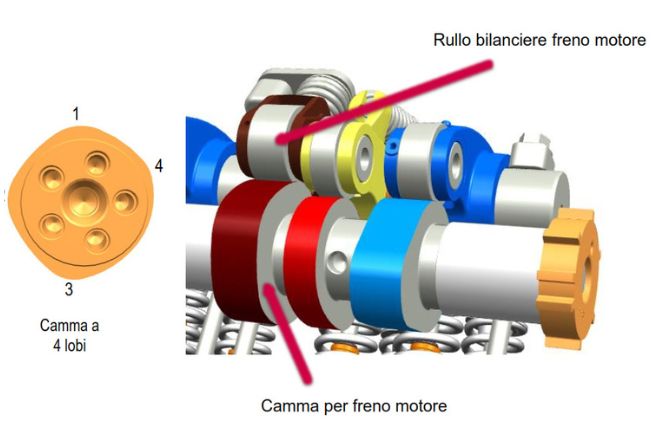
In occasione della presentazione della nuova “teardown area” Fpt Industrial ha approfittato per fare un punto sulle ultime novità di prodotto e sulle più recenti tecnologie applicate. Protagonista tra i motori termici “Xc13”, la prima unità che il brand ha progettato sulla base dei nuovi obiettivi di sviluppo in termini di efficienza, flessibilità applicativa e di alimentazione. Spaziando tra versioni diesel, a gas naturale e a idrogeno. Tra le varie tecnologie implementate sull’unità spicca il sistema freno motore, specifico per le applicazioni heavy-duty. “High performance engine brake”, “freno motore ad alte prestazioni”, il nome del sistema, progettato specificatamente per “Xc13” sulla base del know-how tecnico maturato negli anni sui sistemi di decompressione dei cilindri ad azionamento idraulico. Guardando le curve di potenza e coppia frenanti generate dal motore è possibile apprezzare il contributo che il sistema offre in termini prestazioni. La potenza si mantiene oltre i 500 chilowatt, a ridosso dei 700 cavalli, sopra i mille 200 giri al minuto con una rampa di salita che parte a 800 giri attaccando con 225 chilowatt, circa 300 cavalli, e prosegue quasi linearmente con poco meno di 350 chilowatt, 470 cavalli circa, raggiunti a mille giri.
La coppia frenante invece vede uno sviluppo lineare che attacca a 800 giri con poco meno di 500 newtonmetro e sale fino ad andare oltre i due mila e 600 newtonmetro al regime di due mila 200 giri. A permettere tali prestazioni un sistema di distribuzione con fasatura variabile delle valvole di scarico realizzato giovandosi di due bilancieri, uno “canonico” di scarico e uno dedicato a far lavorare l’unità in modalità freno motore. I due elementi si alternano durante il funzionamento dell’unità nell’azionare le valvole di scarico risultando inseriti nella testata mediante un albero porta bilancieri realizzato in due pezzi.
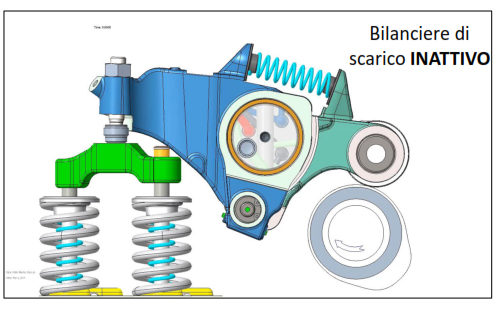
A comandarli provvede un classico albero a camme e a ciascun terzetto di cilindri quindi è associato un albero porta bilancieri dedicato con il primo semiasse che azionale le valvole dei cilindri 1, 2 e 3 e il secondo quelle dei cilindri 4,5 e 6. A ognuno dei cilindri sono quindi dedicati tre bilancieri, due sul lato scarico e uno sull’aspirazione, al posto dei canonici due. Quello dedicato alle valvole di aspirazione vede caratteristiche simili a qualsiasi altro bilanciere utilizzato su motori per applicazioni industriali mentre quello che regola lo scarico, è caratterizzato da un’architettura che rende possibile l’annullamento del movimento generato dall’albero a camme sospendendone di conseguenza il funzionamento ogni volta che la cosa si rende necessaria. Possibilità realizzata grazie a una struttura che vede le due parti dell’albero porta bilancieri, un primo corpo sul lato valvola e un secondo sul lato camma, disaccoppiate tra loro a differenza di quando invece il componente è chiamato a lavorare in condizioni “normali”. Ciò grazie a un sistema idraulico-meccanico composto da due pistoncini che normalmente agiscono come perni di collegamento tra le due sezioni dell’albero rendendole solidali, ma che perdono tale funzione quando messi in pressione dal circuito idraulico dando luogo a uno scollegamento fra le due sezioni. A quel punto la sezione lato camma può ruotare rispetto alla sezione lato valvola senza che sia azionata la valvola di scarico associata. Da segnalare la presenza di una molla di richiamo che facilita i riallineamenti delle due sezioni. Il terzo bilanciere è quello dedicato al freno motore. Anche in questo caso si tratta di un bilanciere disinseribile e gestibile quindi on-demand sulla base dell’operatività richiesta. Vede infatti la presenza di un pistoncino oscillante all’interno della testa del bilanciere che modula l’interazione con la punteria della valvola. L’oscillazione può essere eliminata tramite l’interazione di una coppia di corone dentate, una solidale al pistoncino e una al bilanciere.
Le due corone di fatto sono allineate l’una sull’altra e quando i denti della seconda corona solidale al pistoncino sono allineati alle cave della corona dentata solidale al bilanciere l’elemento può oscillare rispetto al bilanciere annullando la spinta sulla punteria della valvola. In modalità freno invece la seconda ruota dentata viene fatta ruotare in modo da permettere l’allineamento dei denti tra le corone e quindi impedendo il movimento relativo tra pistoncino e bilanciere. In questo caso il movimento del bilanciere viene trasmesso alla punteria della valvola permettendo l’apertura. Per quanto riguarda il bilanciere del freno motore l’azionamento è avanzato tramite una camma dedicata che ha una particolarità.
E’ infatti dotata di quattro lobi in quanto le valvole di scarico al ne di assicurare il miglior funzionamento del freno motore devono aprirsi quattro volte all’interno di un ciclo. L’inserimento e il disinserimento dei due bilancieri è avanzato idraulicamente tramite elettrovalvole quindi per ogni semiasse dell’albero portabilancieri c’è un’elettrovalvola di gestione dei bilancieri freno motore e una che gestisce i bilancieri di scarico. Alla centralina motore è delegato il compito di comandare le elettrovalvole per gestire il flusso d’olio cha va ad attivare o disattivare i singoli bilancieri. Il funzionamento di tutto il sistema si basa su due modalità definite “drive” e “freno”. La modalità “drive” identifica l’operatività del motore quando viene richiesta potenza, quindi ad acceleratore premuto. La modalità “freno” invece identifica la condizione in cui il motore lavora ad acceleratore rilasciato. Il bilanciere di scarico in modalità “drive” si comporta come un bilanciere tradizionale e quindi sotto effetto della camma oscilla intorno all’albero porta bilanciere mentre nella modalità “freno” il bilanciere di scarico viene messo fuori servizio. Da sottolineare che quando lavora il freno motore viene azionata solo una delle due valvole di scarico, mentre la seconda rimane chiusa.
Come funziona
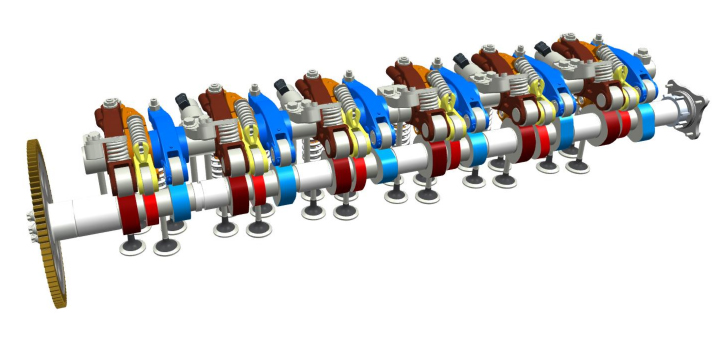
In tutti i motori durante la fase di rilascio dell’acceleratore nei cilindri non viene iniettato gasolio. Quindi nei cilindri c’è solo aria o comunque una quantità minima di miscela atta a impedire lo spegnimento dell’unità. In fase di compressione quindi il pistone comprime l’aria che si comporta a tutti gli effetti come una molla. Si comprime accumulando energia sotto forma di pressione fino al punto morto superiore ma una volta superato la restituisce al pistone spingendolo verso il basso. Il sistema freno motore punta a eliminare questo cuscinetto d’aria e quindi l’effetto “molla”. Di fatto quindi quando l’unità lavora in modalità freno motore il bilanciere dedicato apre le valvole di scarico in quattro punti del ciclo. Le prime due in corrispondenza dell’inizio delle fasi che vedono il movimento ascendente del pistone, quella di compressione e quella di scarico. In tali momenti le valvole di scarico vengono leggermente aperte per richiamare aria dal collettore di scarico che ha pressione maggiore rispetto all’aria che c’è nel cilindro. E quindi il pistone incontra una maggiore resistenza durante la risalita rispetto alle condizioni normali, rallentando. Alla ne della corsa di ascesa del pistone si hanno invece le due fasi “compression release”, ovvero di rilascio della compressione. Vengono aperte di nuovo la valvola di scarico per espellere il cuscinetto d’aria. In tale ottica il pistone non solo non subisce il rimbalzo indotto dall’aria ma deve opporsi alla pressione negativa che si crea quando si avvia il movimento discendente prima dell’apertura delle valvole di aspirazione.
Titolo: Freno motore Fpt “Xc13”, alte prestazioni ed efficienza
Autore: Redazione